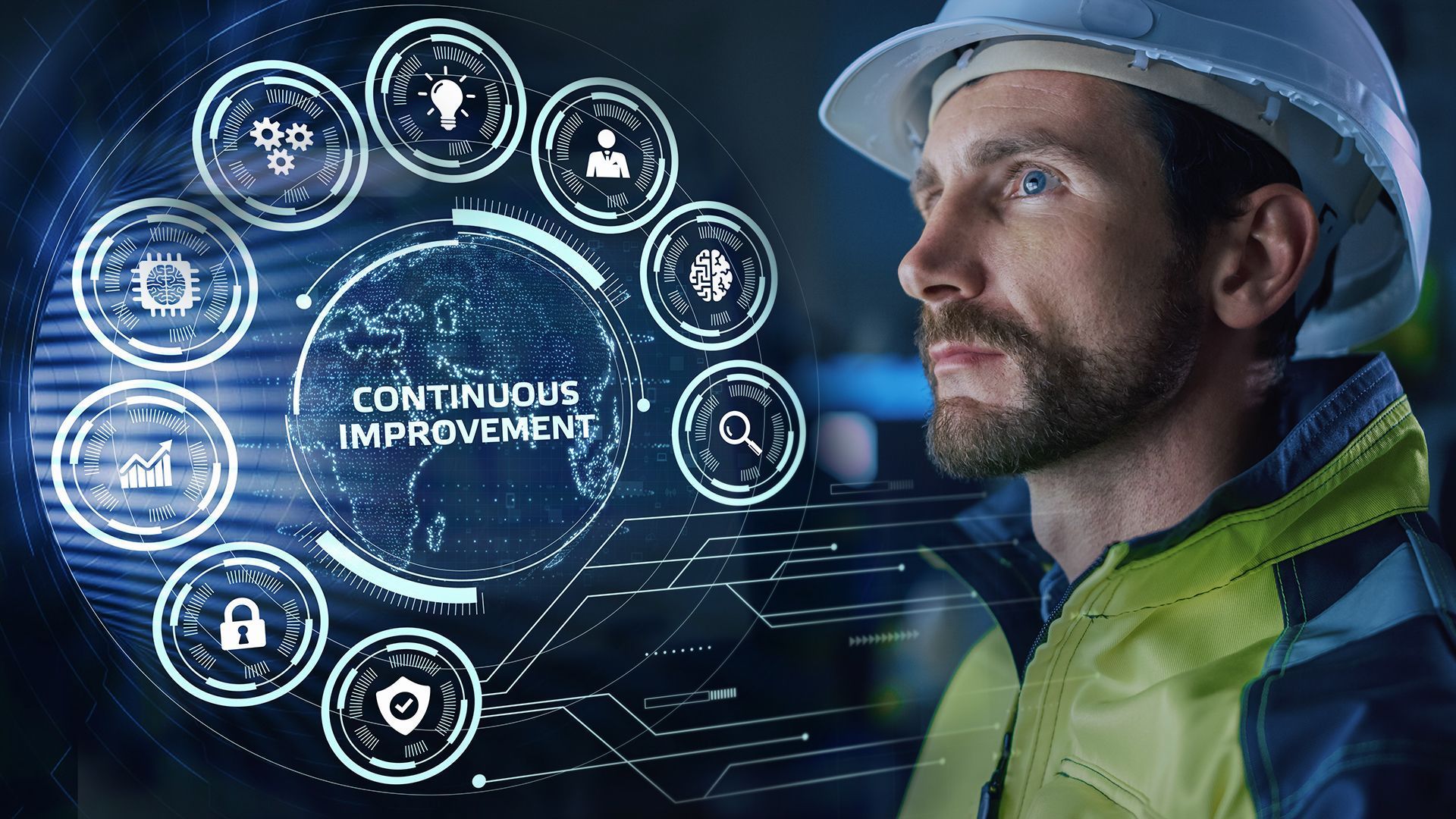
- November 22, 2021
- admin
- 0
5 Key Steps in Continuous Improvement in Manufacturing
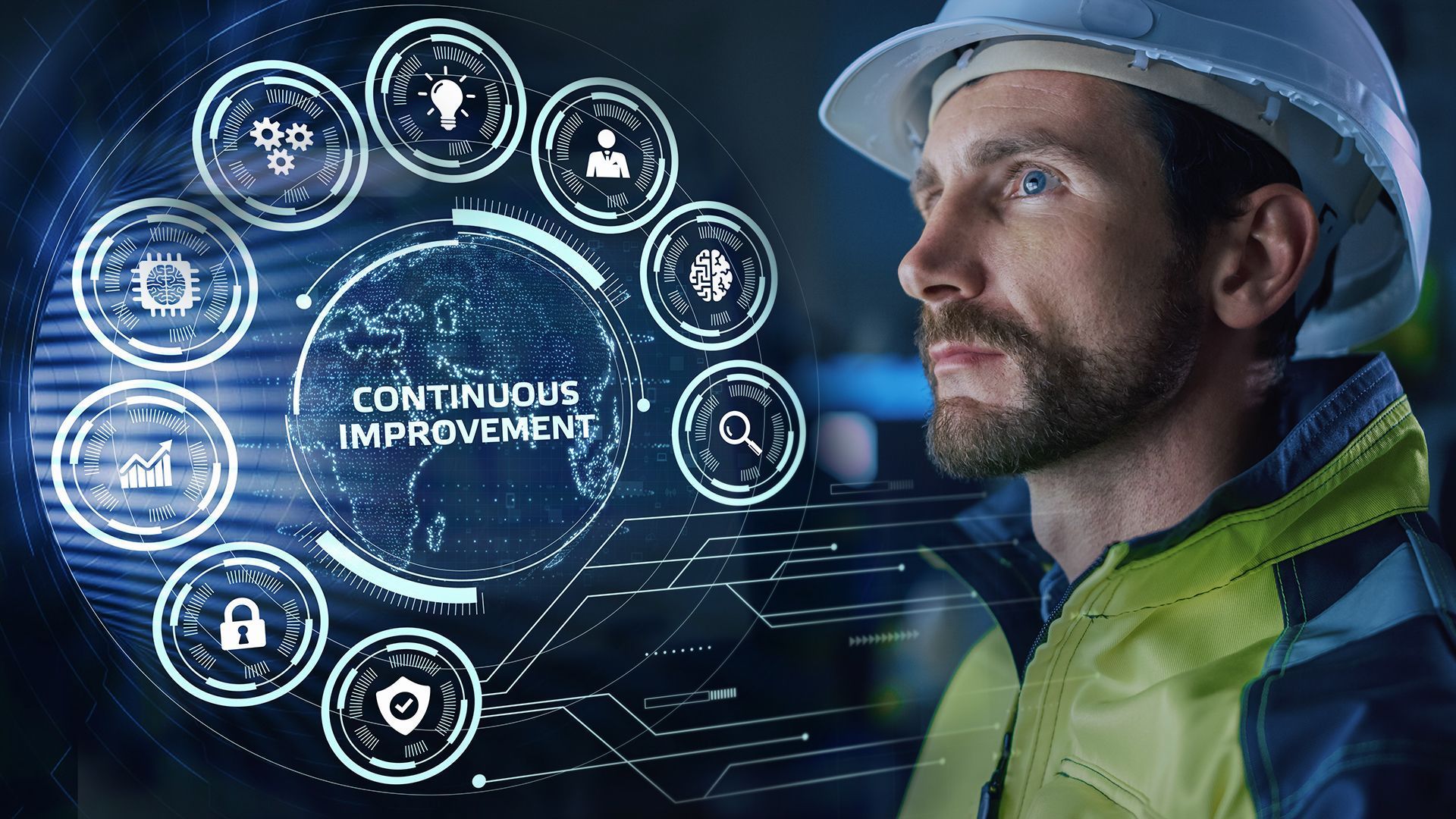
Continuous improvement in manufacturing industry is the continual improvement of products, services, or processes through tiny yet breakthrough improvements. This linear and incremental improvement deals with a single step. Manufacturers can adopt multiple ways to improve the production process incrementally. Experts believe that these changes may not have a significant impact on the result of that particular step. They further agree that the aggregate can show remarkable change and improve the overall production process.
This blog provides a clear picture of continuous improvement, different steps in this process and how lean manufacturing is different from this improvement.
The process of continuous improvement in manufacturing involves the manufacturers taking small incremental and measured steps every working day. It ensures improvement as it eliminates the risk of adopting one massive change to gain the same effect. The optimum goal of this change is for
- Efficient production
- Reduce wastage and unscheduled interruptions
- Eliminate unnecessary steps
The result of this tiny multi-step change is to have optimal automation and standardize the production process. Building an atmosphere of continuous improvement in the manufacturing industry requires the management to create and work on a customized strategy, as per the organization and working conditions. They can also look towards lean manufacturing. Experts suggest that manufacturers should take care that tailor-made strategies to align well with the existing manufacturing model, process workflow and operational functions of the organization.
What is Lean Manufacturing?
Lean manufacturing is a reduction technique in which the management focuses on eliminating waste. It further includes reducing and controlling production costs to increase efficiency, profitability and value to the customer. It aids companies to achieve improved flexibility, sharpening the production process and increasing output by reducing production costs.
Difference Between Lean Manufacturing And Continuous Improvement
Lean manufacturing aims at reducing wastage, which could be a short-term cost-saving strategy. In a few cases, the management can hire skilled workers to achieve the same. It can lead to overworking staff, leading to dissatisfaction among employees or less-skilled employees taking longer time to complete a task. Such situations can further lead to a risk of workplace injuries or conflict between management and the production team.
Continuous improvement in manufacturing includes tiny steps that start from the base and move upwards. It includes encouraging floor employees to identify and find solutions to improve the production process. It will help the management, as employees will feel more valued; thus, reducing the gap between the management and production employees. This technique has greater chances of success as workers would readily accept the changes suggested by their colleagues.
Steps For Continuous Improvement
The essential component of manufacturing operations management is continuous improvement. A well-planned process provides vital structure to build a resilient manufacturing unit. It can eliminate waste processes, streamline operations and produce a better quality product at a lower cost.
The different steps involved in continuous improvement re:
- Identification of overall objective
The initial step in this process is, to begin with, the current state and understanding of the present scenario. The management needs to focus on a few parameters like
- Identifying key performance indicators
- Comparison between present manufacturing performance and future expectations
- Type of improvement required to achieve the goal
- Discovering core competencies and finding qualified personnel to achieve the target
- Identifying performance metrics
- Defining continuous improvement process
Every part of the manufacturing process is entrusted to one personnel, who keeps track of the performance and maintenance of the equipment. The concerned staff would be the best to suggest steps to enhance performance. The concerned floor manager needs to explain the change so that everyone is aware of it. Management can keep track of the responsible person and check if everyone on the floor is working towards a continuous improvement plan.
- Deploying proper tools and communicating effectively
This type of change is not a natural phenomenon, and the manufacturers need to put in extra effort to convince employees to adopt the change wholeheartedly. The management needs to educate them about the process and benefits of including the new technology in their work culture. On-going training and education initiatives are a few measures that could provide desired results in this regard.
- Measuring outcomes
The positive outcome of a continuous improvement program is possible only if the plan is realistic, achievable and relevant. Quantifying these characteristics will help to understand if the program has worked or not. Positive outcomes will motivate the management to invest more resources for future expansions.
- Implementation of digital improvement
The use of digital technology makes continuous improvement easier. Artificial intelligence aided programs provide more effective results, as they can monitor tram performance, the overall impact of the change, and the resources that have significant value in the industry. Access to real-time data helps the manufacturers to act on time and take corrective measures.
Latest technologies like artificial intelligence help build new models with available data. These algorithms help in the easy and quick implementation of continuous improvement in the manufacturing process. In most cases, the manufacturers experience improved models that provide desired results on the floor.
Categories
Recent Posts
- Types of Waste in Food & Beverage Manufacturing and How to Eliminate Them
- 5 Proven Strategies to Reduce Downtime in Your Food & Beverage Plant
- The Ultimate Guide to Digital Transformation in Food & Beverage Manufacturing
- Adapt a Continuous Improvement in Manufacturing to Cut Unproductive Work
- Artificial Intelligence and the Success of Industry 4.0